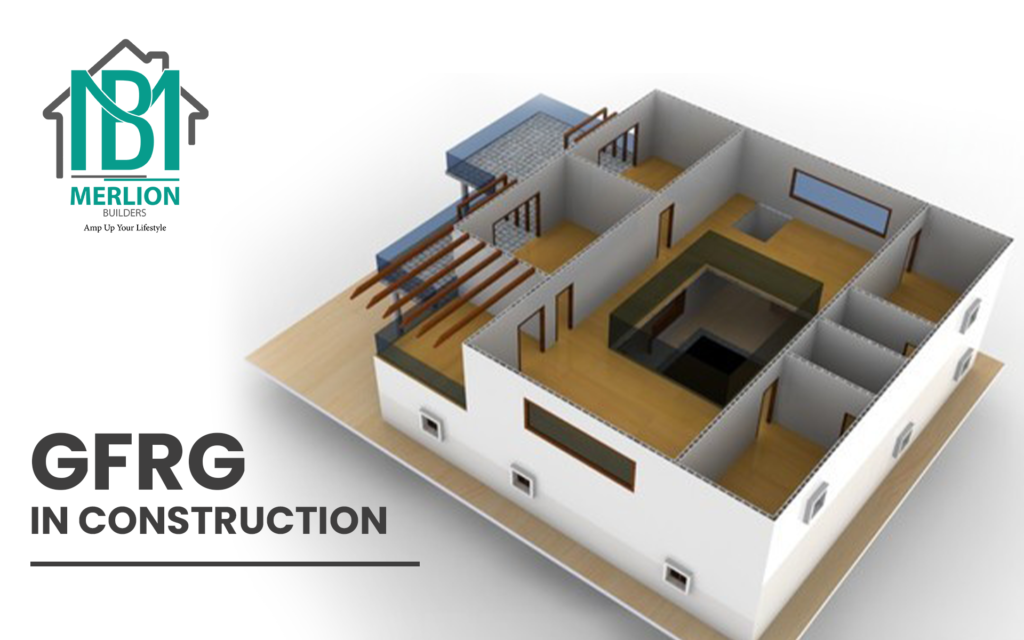
Construction in real estate is getting modernised with the use of technology. Innovative and high efficiency building materials are being used in construction that provides strong and durable housing at an affordable cost. One such sustainable solution is GFRG, Glass Fibre Reinforced Gypsum panels.
1. What is a GFRG Panel
GFRG stands for Glass Fibre Reinforced Gypsum which is developed in the form of panels and then used in construction. This is an efficient building construction material known for its durability. GFRG panels, also known as Rapid walls, are made up of gypsum plaster which is known for its durability and overall appearance. High-strength and resistant glass fibres are bonded with high-density gypsum cement to create these panels. This is a new technology in the construction sector. As the usage of cement and sand is reduced in a GFRG Panel building, the carbon footprint also gets reduced and contributes in saving the environment.
2. Technology Behind GRFG Panels
This technology comes into action after the foundation is placed, using advanced methods. These panels are manufactured in factories and then brought to the construction site. When the foundation is ready, these panels are placed on it with the help of cranes. A unique form of locking system is used to grip the ribs of the panel on top. Walls created with GFRG Panels do not require any plastering and painting as a normal wall would need. They panels, actually replace the use of blocks or bricks which are normally used for constructing the structure of a house or a building.
3. Know More About GFRG Panels
GFRG Panels are fabricated in semi-automatic plant using slurry of calcined gypsum plaster mixed with
certain chemicals. It also includes water repellent emulsion and glass fibre rovings, cut, spread and imbedded uniformly into the slurry. A screen roller is used for the same. These panels are then dried at a temperature of 275 degrees Celsius. When dried, they are shifted to storage area or the cutting table where the panels are cut as per the dimensions and requirements of the building.
Each GFRG Panel is manufactured under carefully controlled conditions, with a thickness of 124mm and a length of 12m and height of 3m. As per the structural demand, the cavities of these panels may be unfilled, partially filled or fully filled with reinforced concrete.
4. Features of GFRG Panels
Every coin has two sides, i.e. the pros and cons. Similarly GFRG Panels also have a number of advantages followed by a few limitations, which one has to be careful about.
4.1. Advantages of GFRG Panels
4.1.1. Increased Speed of Construction
The GFRG Panels are manufactured at a unit which is away from the construction site and then brought to the site for assembling. The construction timeline decreases because GFRG Panels have only to be assembled at the site.
4.1.2. Lightweight and Cool
Due to their light weight, they reduce the load on supporting beams and pillars of the building. As we all know, concrete heats up the building in high temperatures but GFRG Panels can help to keep the building cooler by up to 4 degrees.
4.1.3. Holds Resistant Features
GFRG Panels are Fire-Resistant, Water-Resistant and Earthquake-Resistant. If there is a fire in the building which is constructed with GFRG Panels, then these panels release 15-20% moisture of their own weight. This decreases the surface temperature and also the fire damage to that building. These are Water-Resistant due to the presence of several chemicals that are added to the mixture during the manufacture of these panels. They are also Earthquake-Resistant and due to this factor, they are used in shear wall construction, an important feature for high-rise buildings. Due to its excellent thermal efficiency, the expenses for cooling and heating get reduced.
4.1.4. Economical and Durable
If GFRG Panels are being used in the construction of a building, then the usage of conventional building materials gets reduced, such as cement by almost 50%, steel by 35% and sand by a surprising 76%. Hence it becomes economical and convenient too. These panels are five times stronger and durable than conventional construction materials because gypsum offers great dimensional stability and strength and is known for its durability. It saves time and money. These panels need little to no maintenance and boast a long lifecycle.
4.1.5. GFRG Reduces the Cost of Construction
GFRG is a cheaper alternative as compared to concrete and bricks. The main component used in the construction panel is a powder that is the leftover of a number of fertilizer industries and is available at a very cheap rate in the local market. GFRG panels are easy to assemble and take less time to dry. Hence the construction time gets reduced. Not much labour is also required, thus reducing the cost of construction.
4.2. Limitations in Usage
There are a few limitations with the use of GFRG Panels. They need to be stacked precisely to minimise deformation, damage, and abrasion. They have to be placed vertically on the support that extends the whole length of the panel. They should be moved slowly and carefully to avoid excessive dropping, cracking, or damage to the sides, edges, and corners. They need to be handled carefully. Appropriate equipment should be used to cut the GFRG Panels. Loading, transporting, and unloading GFRG panels also require extreme precautions.
5. GFRG Panels in ConstructionGFRG
Panels recognized as Rapid Walls, stand for Glass Fibre Reinforced Gypsum and made up of high strength resistant glass fibres bonded with high-density gypsum cement. This is a modern technology which is being used for mass-scale construction of houses in a very short span of time. These panels have a glazy surface and are white in colour. They are considered to be energy-efficient green building material. They have enormous potential and are used as load-bearing and non-load bearing wall panels. These are used in both, external and internal walls and are also used as an intermediary floor slab/roof slab together with Reinforced Cement Concrete (RCC) as a composite material. GFRG Panels are also used on the floors, sunshades, boundary and roofs. These have high flexural strength, shearing strength, compressive strength, and flexibility with a high resistance to fire, water, earthquake and heat.